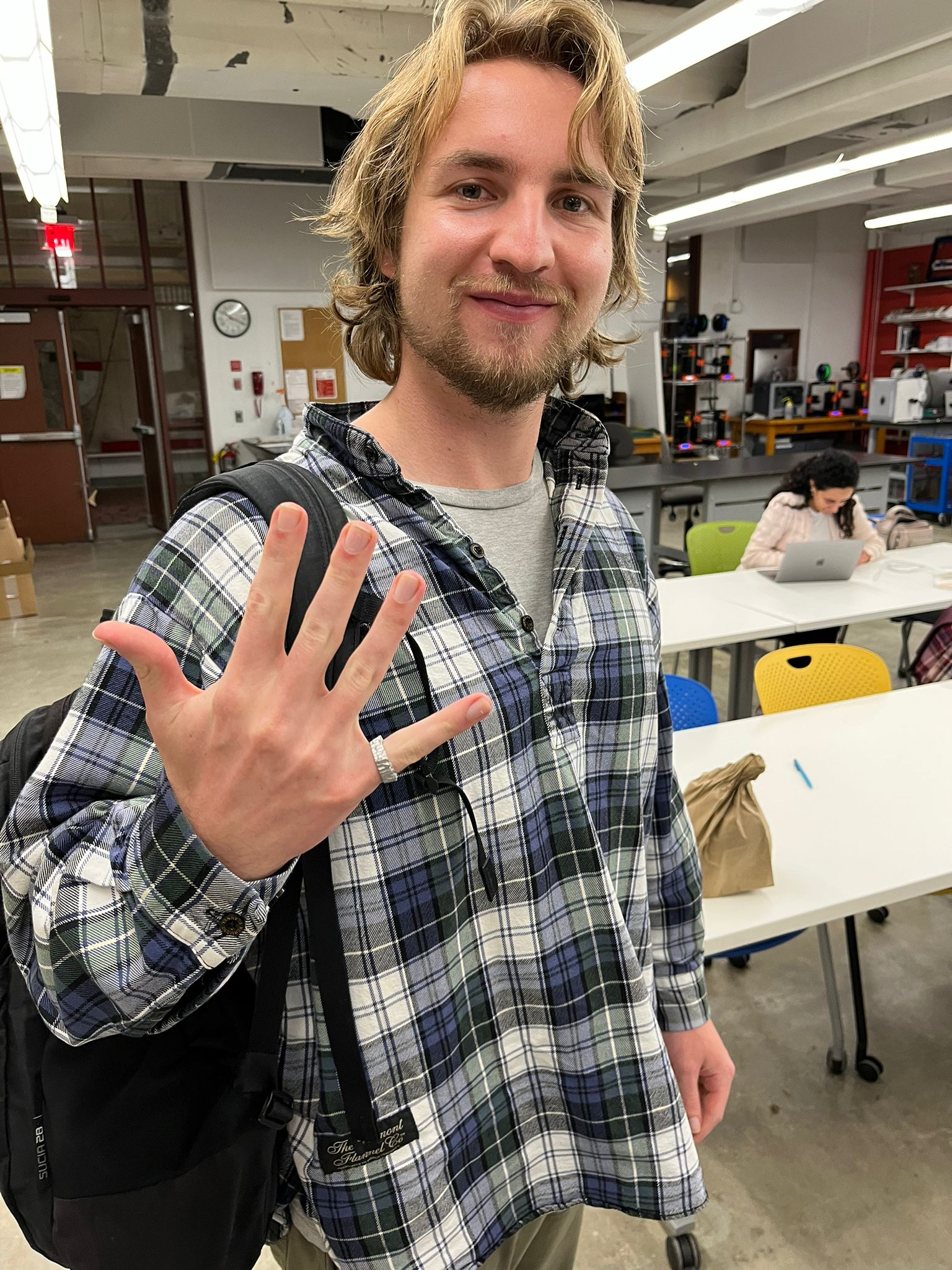
Ring
To make sure I had a finished product for the week I decided to make a cool ring. I wanted to put shapes on the ring. I originally started by using octagons but realized that the mill could not make undercuts easy, so I decided to use triangles. Both of the SRM-20 were being used so I tried to figure out how to use the shopbot. The shopbot in the lab I only knew how to use Aspire with. So I tried to figure out how to mill 3d with Aspire. It ended up being much easier than I expected.Aspire
- Open up a new file
- Load in the measurements of the wax block
- Import STL file
- Orient it to fit in area
- In toolpaths go to rough cuts
- I used the speeds and feeds from an old fabacademy website I found
- Then go to toolpaths go to finish cuts
- Change mill bit to 1/16th follow the same fabacademy websitefor speeds and feeds
Shopbot
- Change collet such that it can fit smaller mill bits
- Turn on machine
- Move to the correct corner of wax block
- Set X and Y to zero
- Air cut
- Using paper method, drop down mill bit
- Run rough cut
- Change mill bit
- Run finish cut
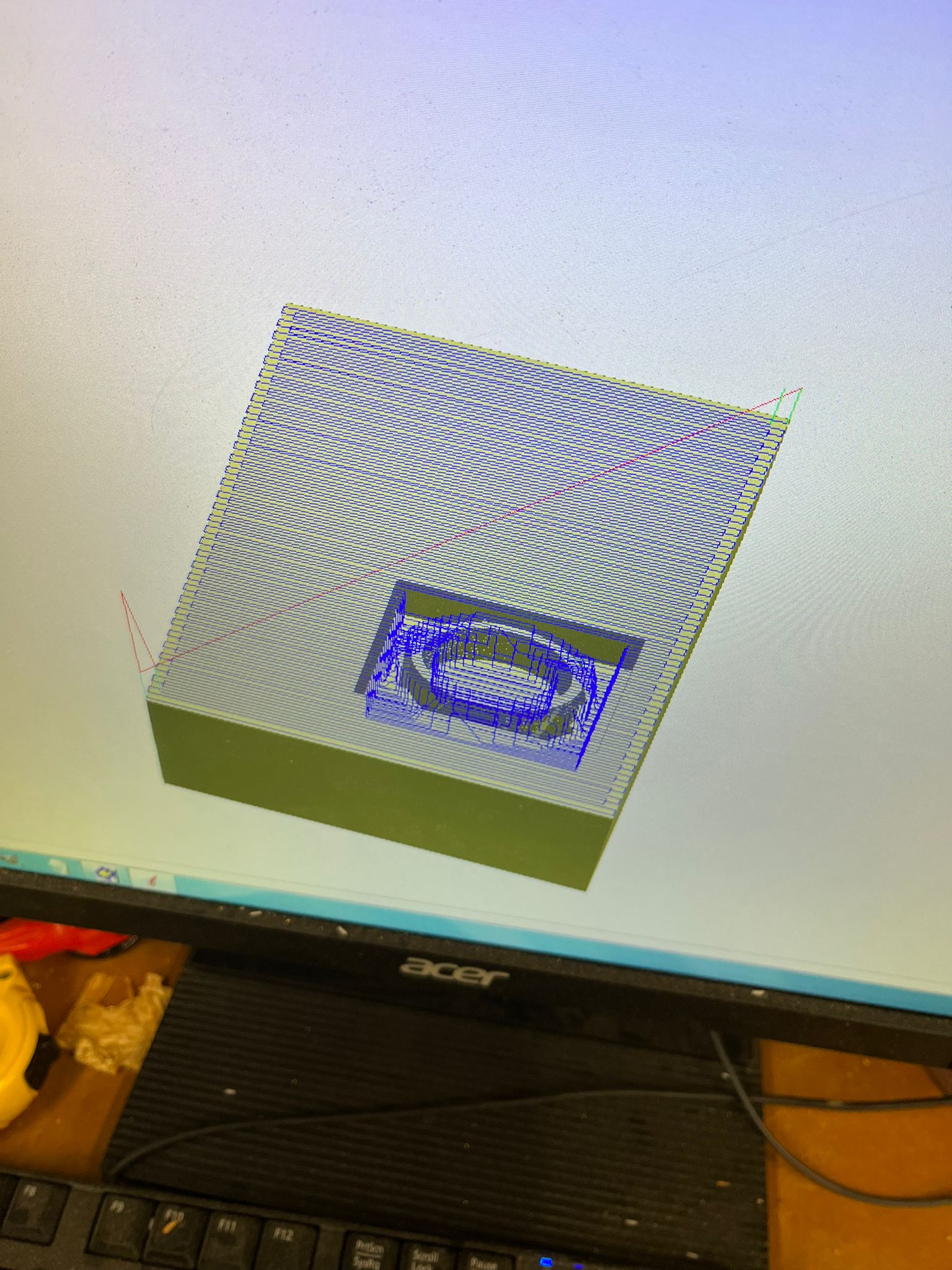
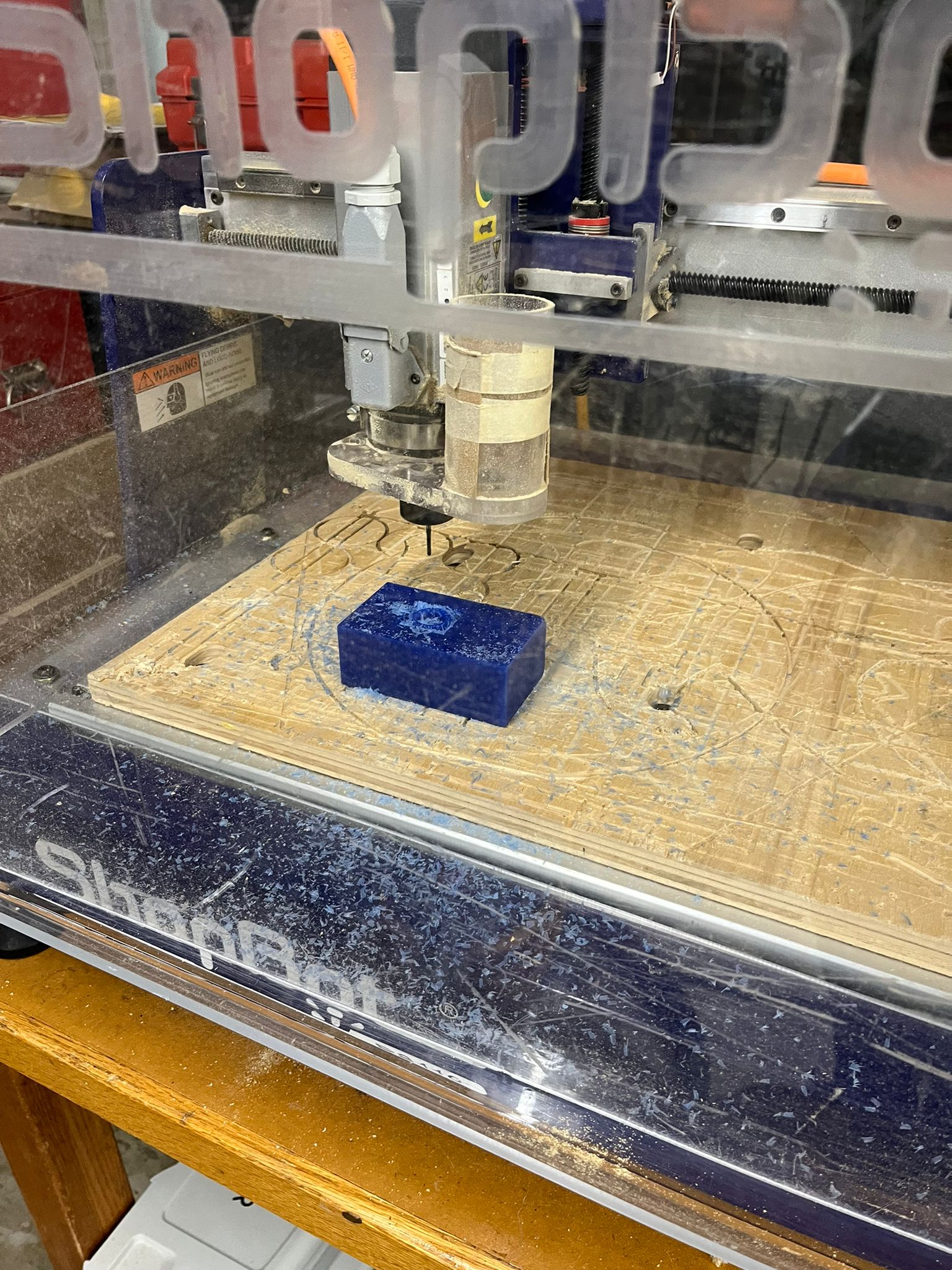
Casting with Bismuth Tin alloy
- Preheat toaster oven to maximum value
- Put metal in metal container in oven
- Once heated pull out with an oven mitt
- Pour into mold
- Once poured you are able to move the metal around very easily so if you mess up either pour metal off by tilting or use something to move it around
- Let sit till cooled
- Shave off any extras

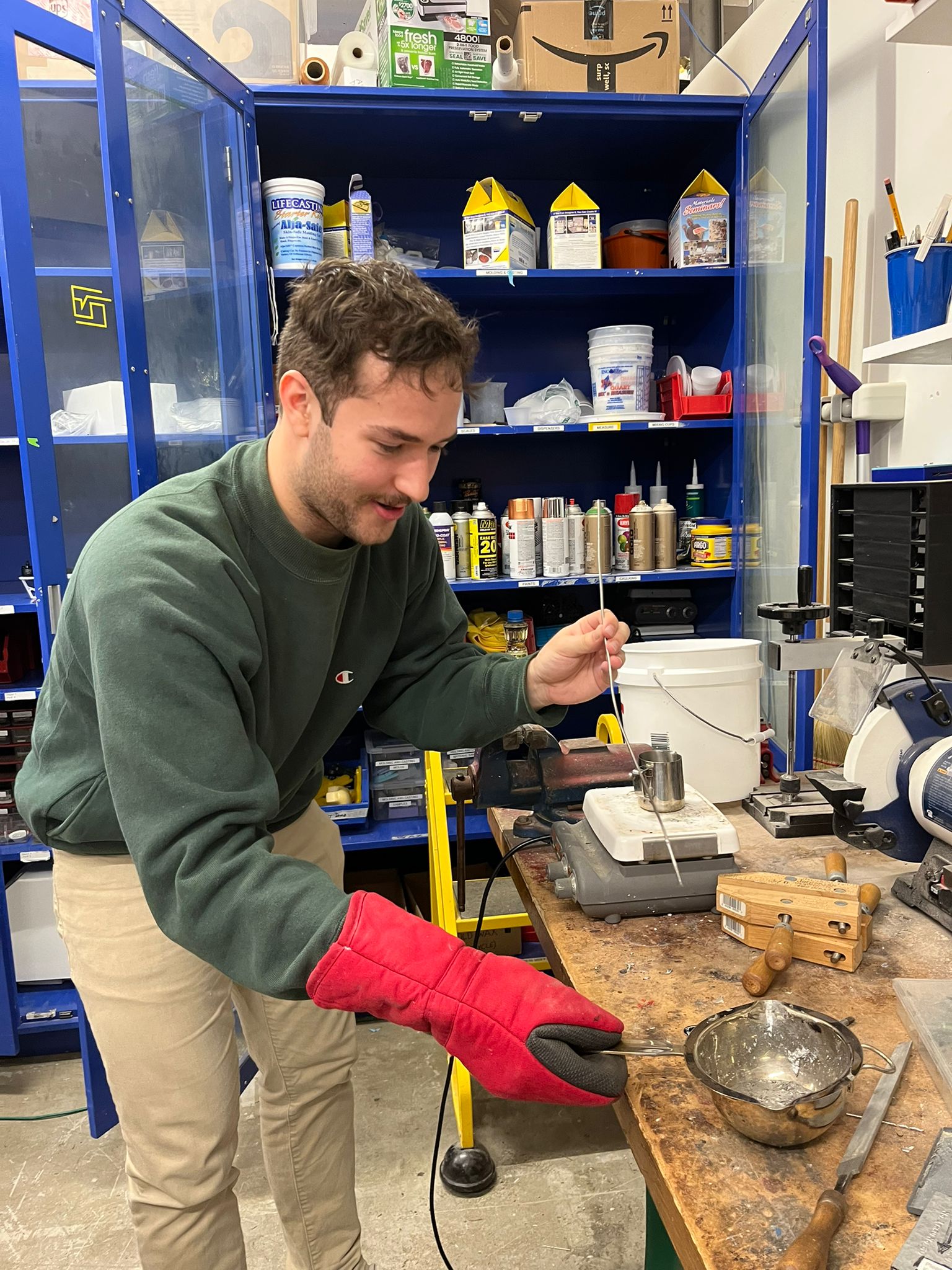
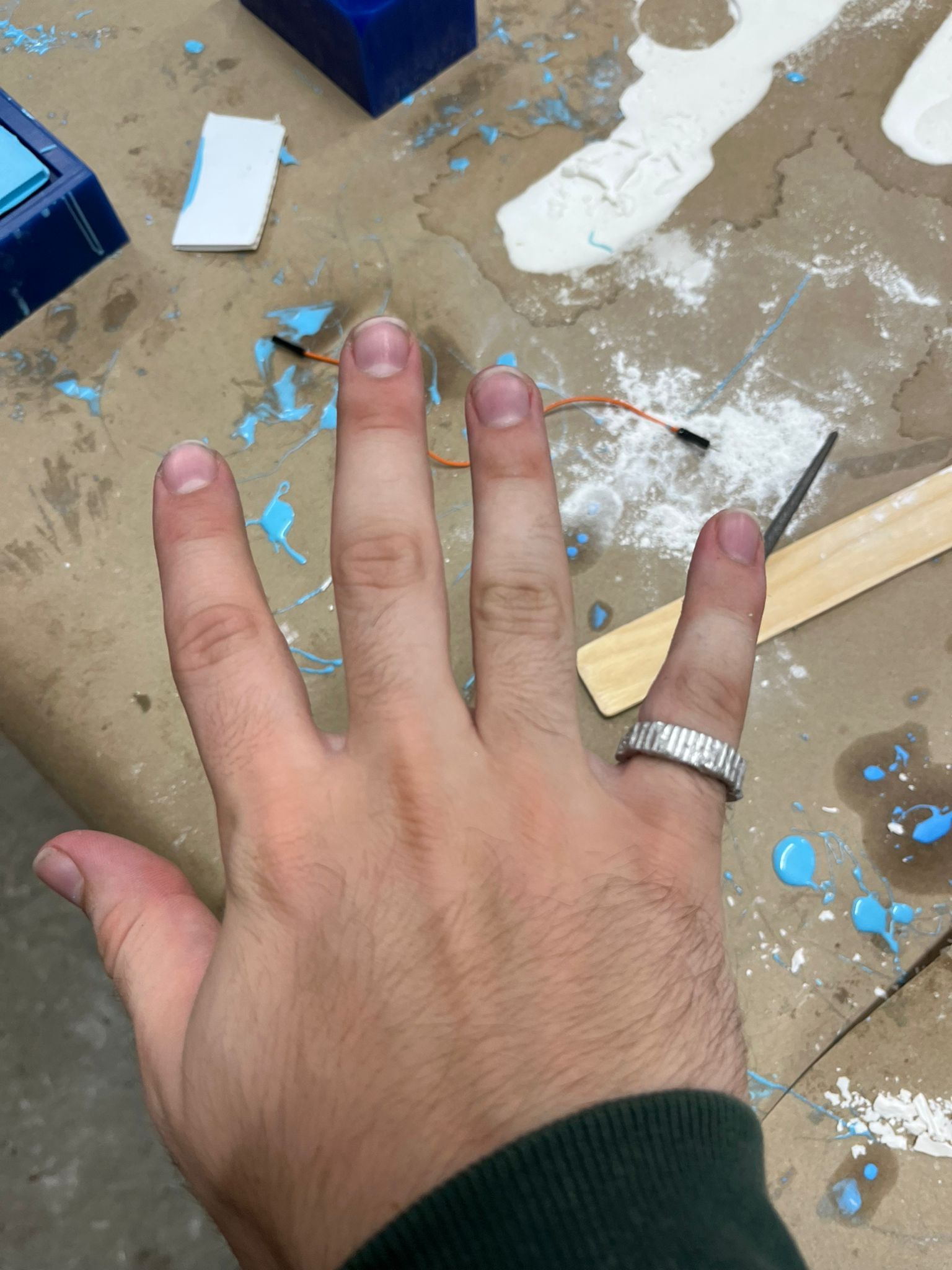
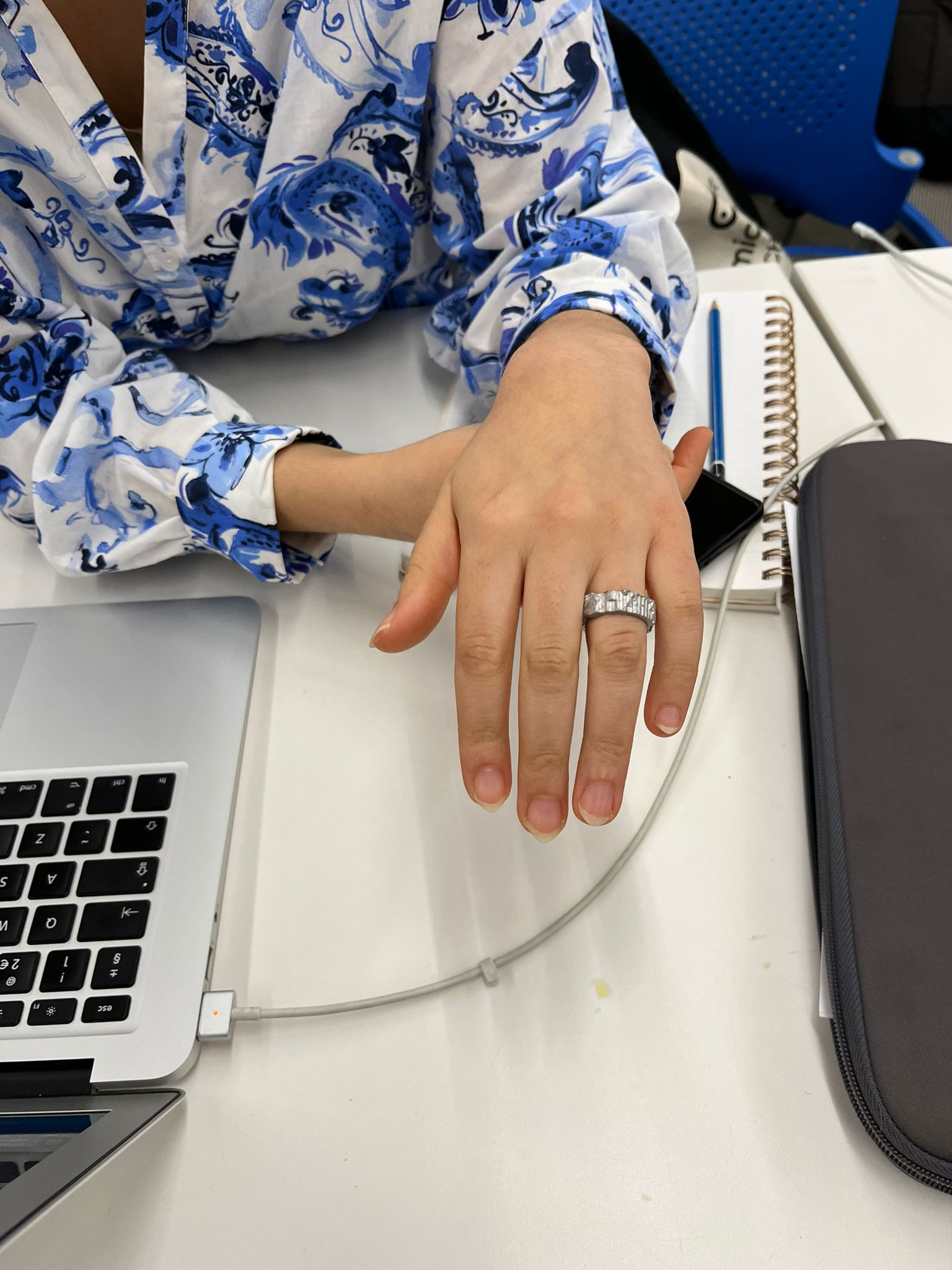
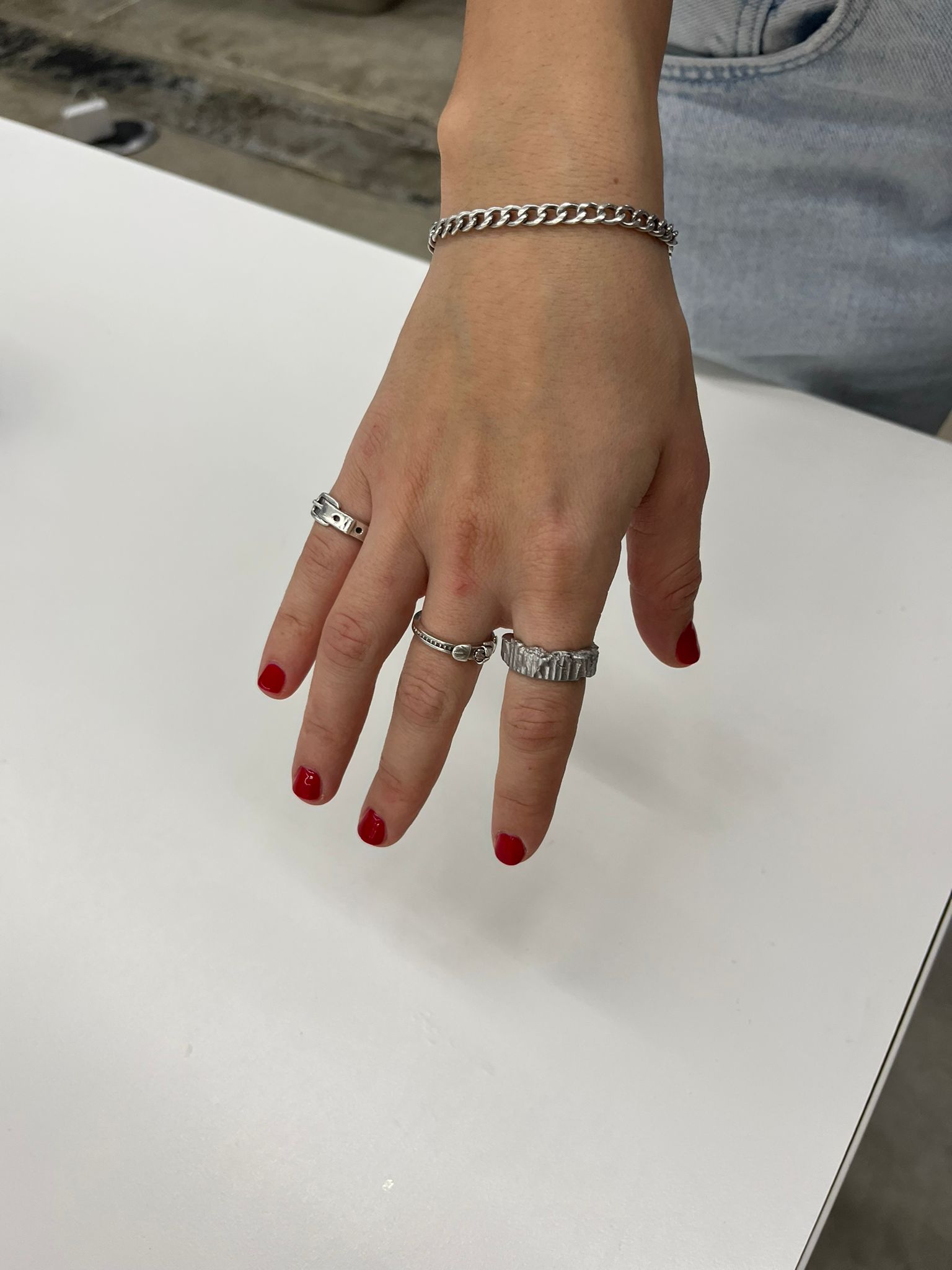
Nose
My idea was I want to see which was better, a cast of my nose or a revopoint scan. I started off thinking that I make a cover of my own nose for my final project. I decided to do two things to try to see what ended up better. I started off by using aljenate to take a mold of my nose. Because I didn't want it to go up my nose I put paper towls in my nostrols.Aljenate
- Follow Alja-Safe Instructions on how to use the molding gel
- Mix ration 1:1 Alja-Safe to warm water
- Find flexible mixing container
- Put powder in
- Start gradually pouring warm wating into center of powder while mixing
- Mixing spread on walls in order to make sure all the powder is dissolved
- Once you reached a good consistency pour into container
- Good consistency means doesn't fall off stick
- 5 minutes to mix
- Stuff your face in it
- Wait fro 8 minutes or until firm
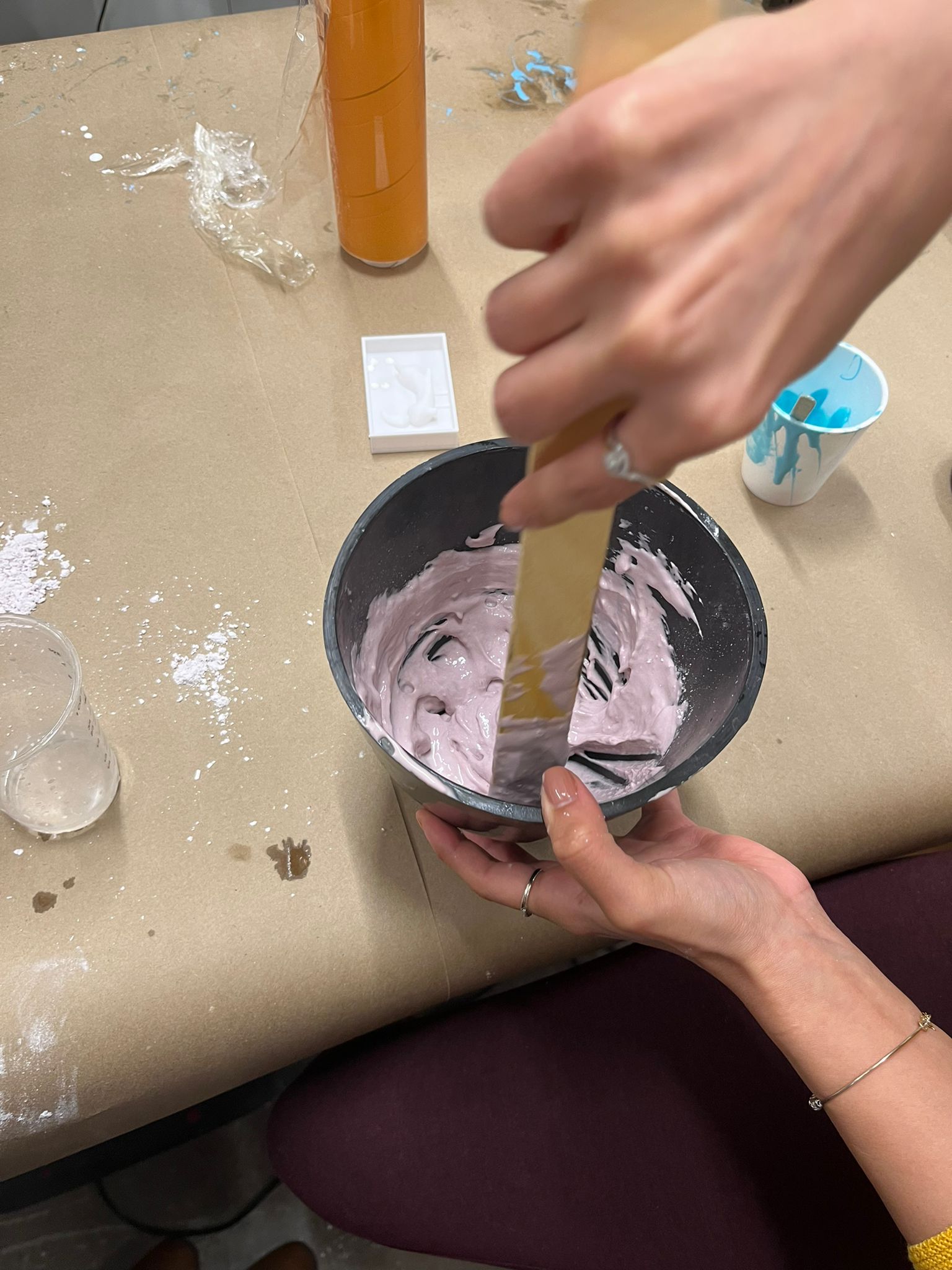
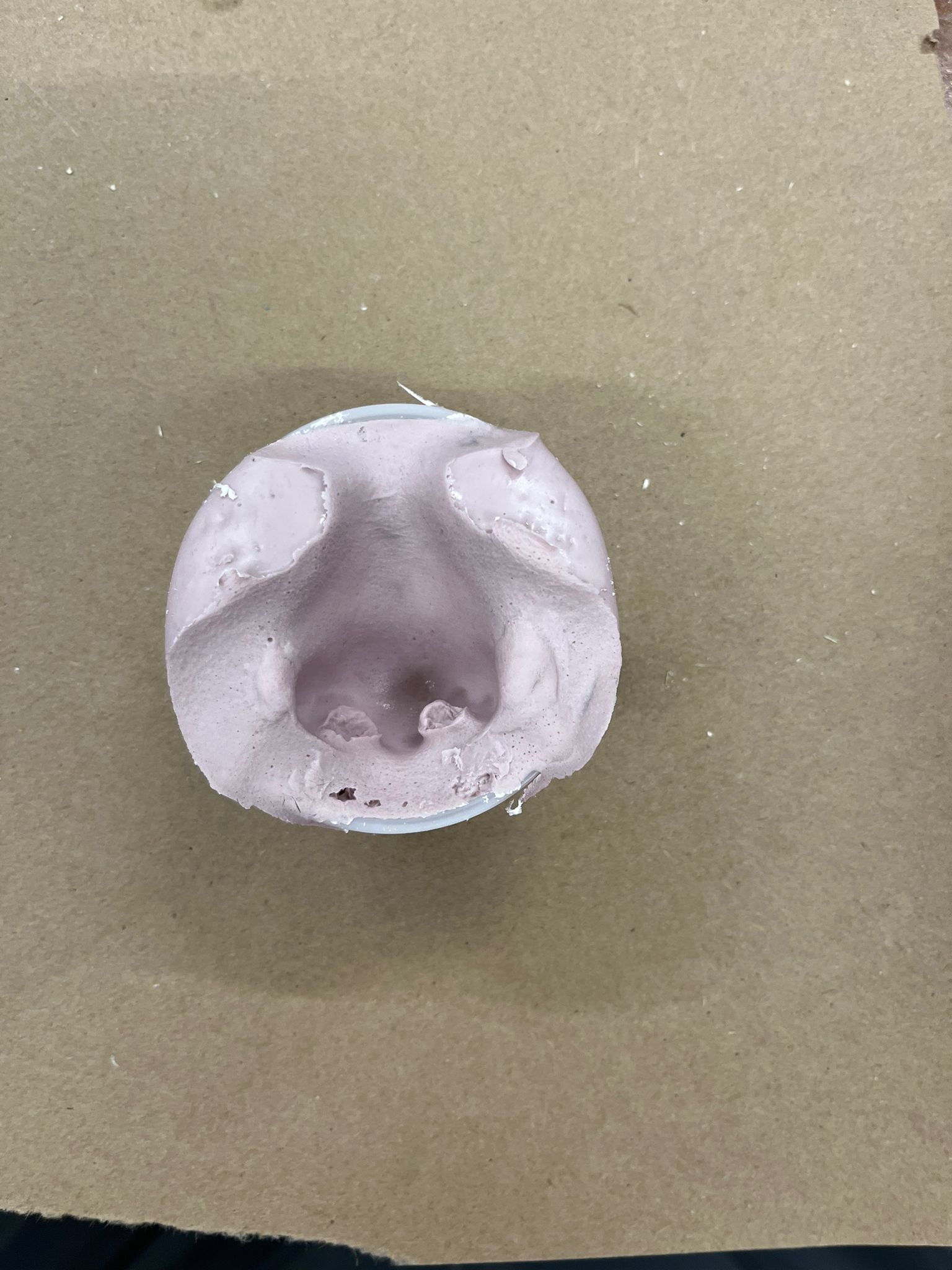
Gypsom Cement
- Follow Gypsom cement intructions
- On box it says to use 100:65 ratio of cement to water, this worked but it took a long time to dry. Other people were doing much more cement and making the consistency thicker. Both seem to work fine
- Always start with water
- Then start pouring cement into the middle and continuously mix, using a flexible bowl is nice to we can mix on the sides
- Make sure to get any cement mix on the sides, Sondos (resident gypsom expert) said to push the sides in order to make the mix better
- Once consistency is flows off the mixing utensil pour into mold
- Wait overnight
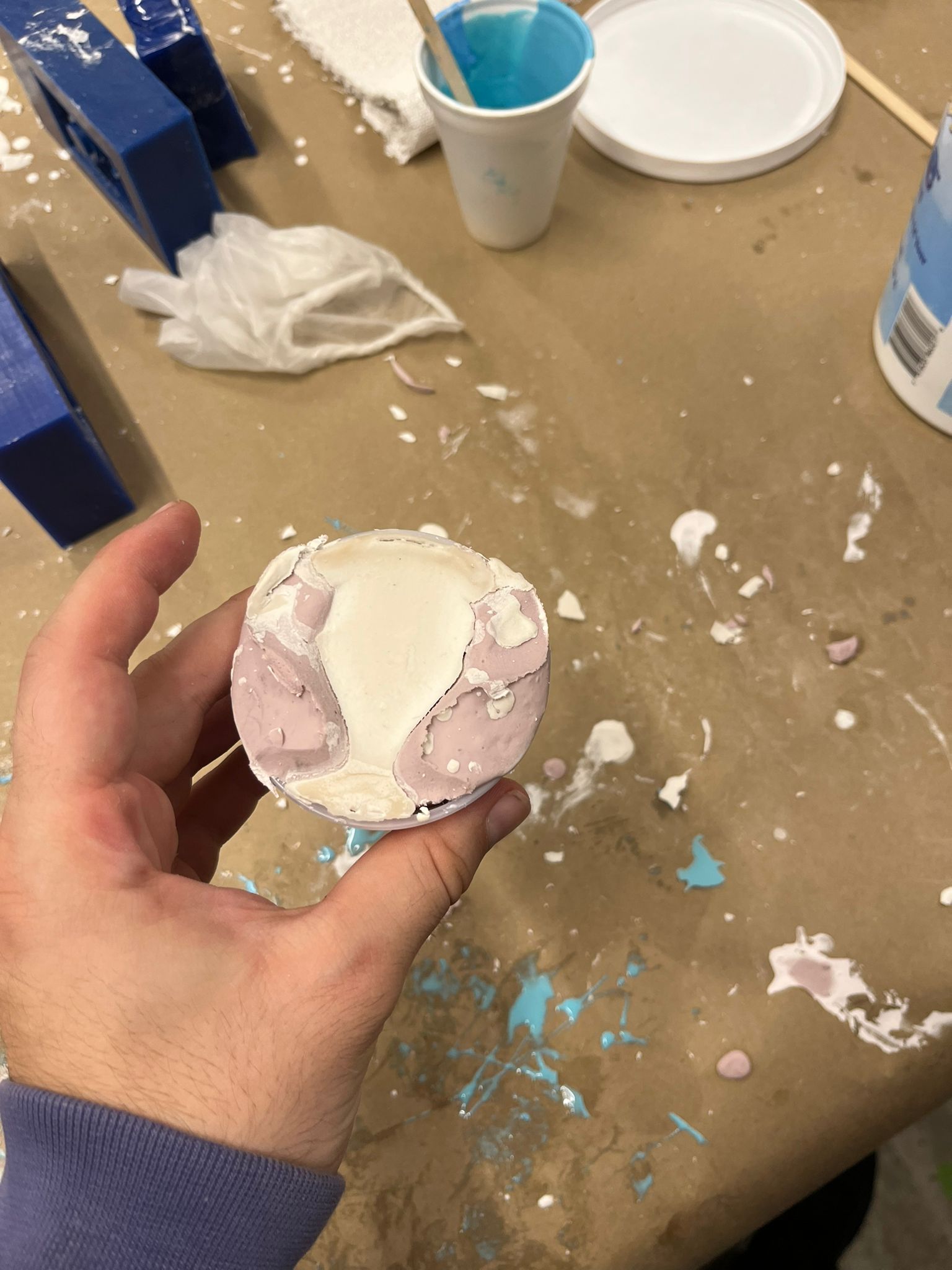
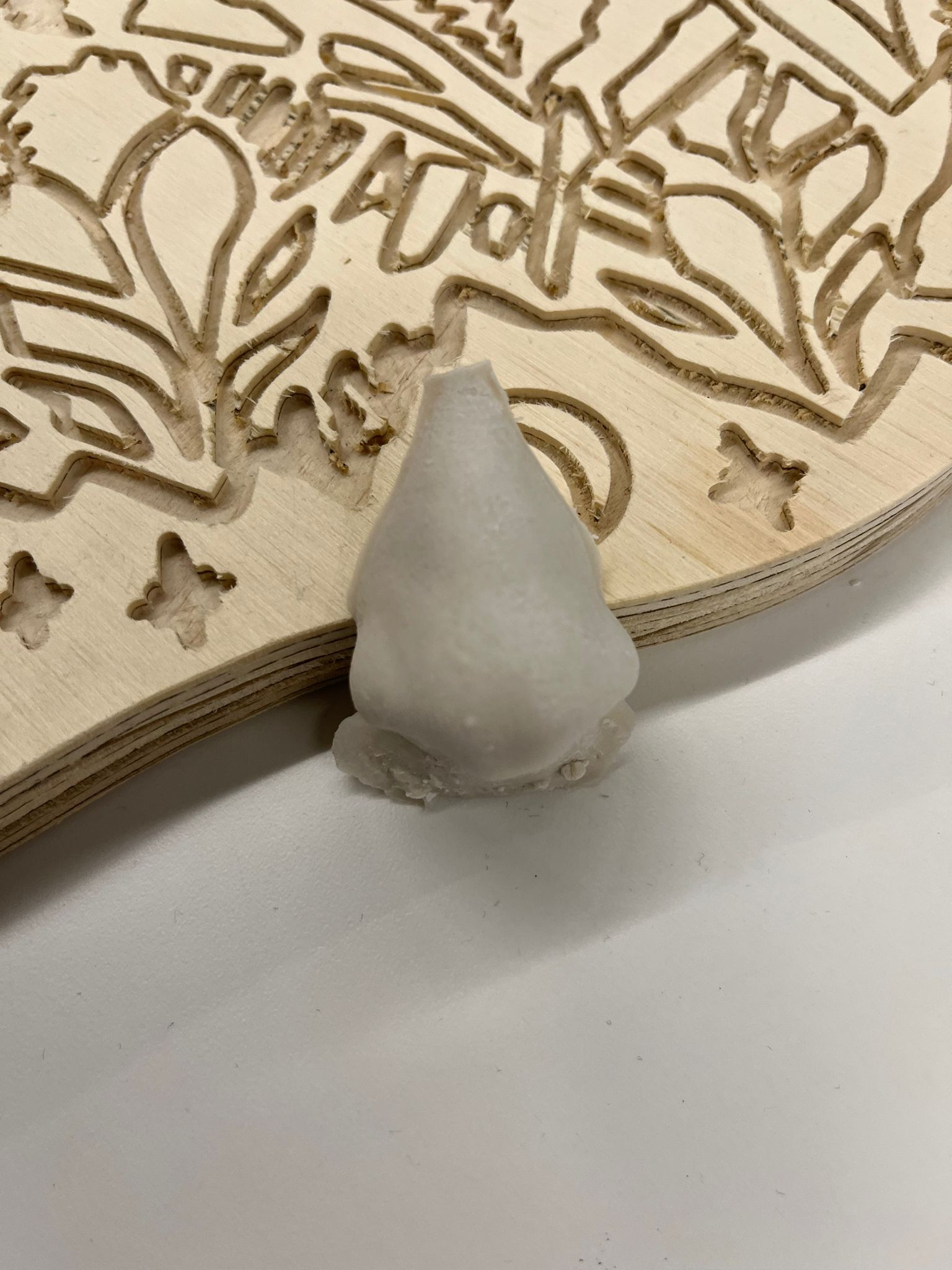
Revopoint
- Open Revo Scan
- Hit Scan
- Accuracy set to High Accuracy Scan
- Scan Mode set to Face, I tried head but I got a better result with face
- Texture set to Color
- Hold camera at distance where Revo Scan says excellent
- Scan Face
- Fuse
- Mesh
- Export
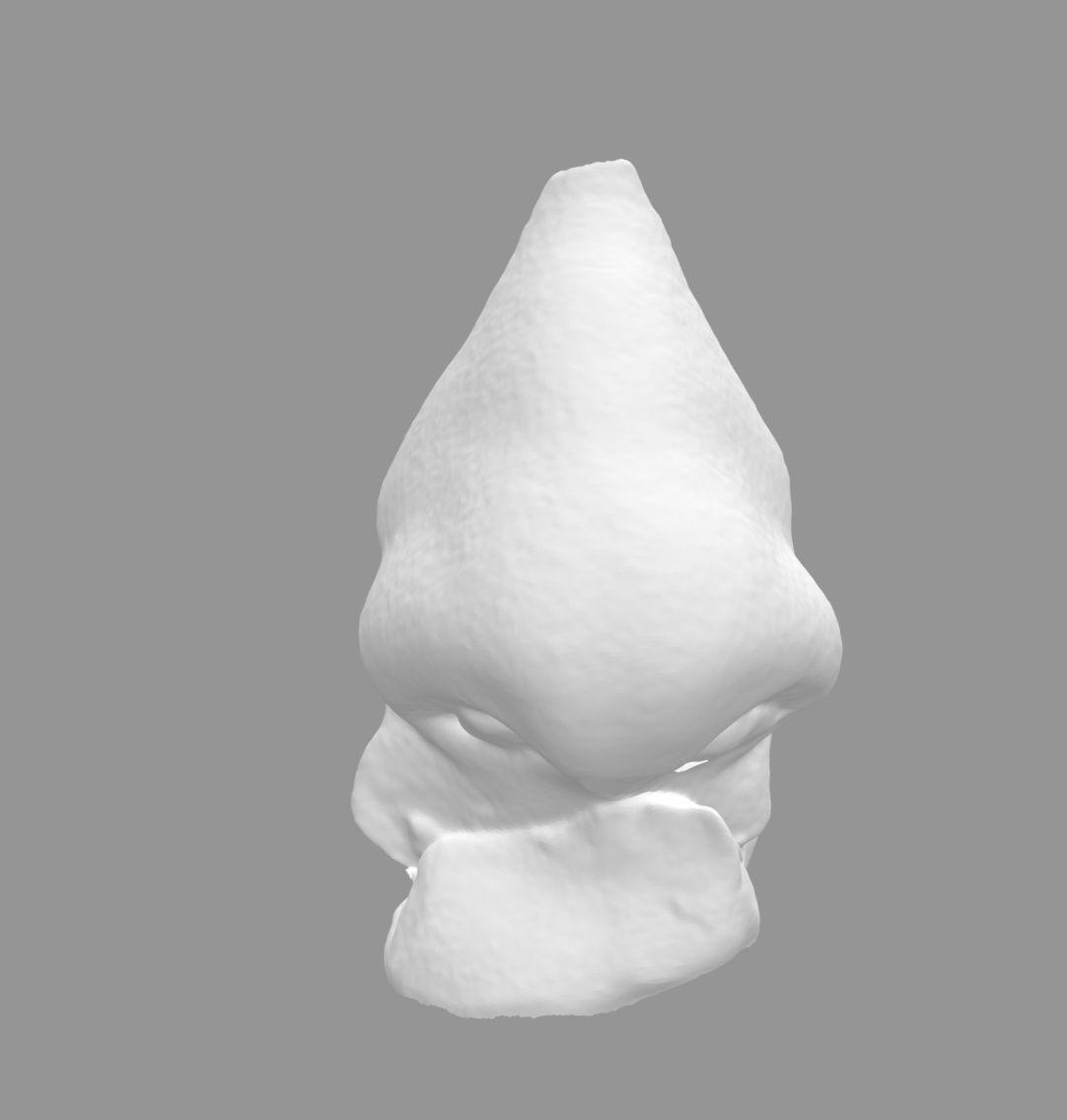
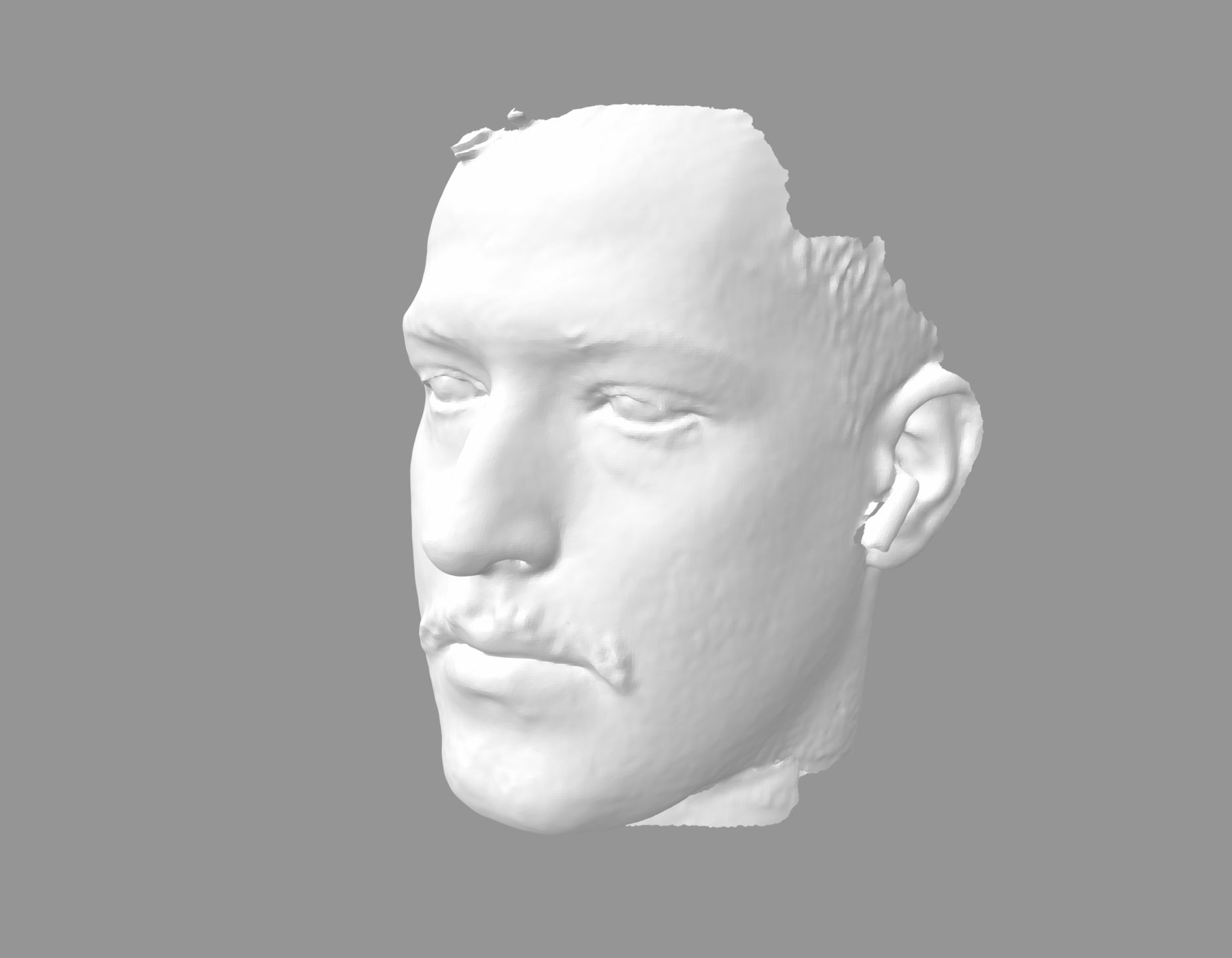
Proof of concept
In order to get a proof of concept of how to get a uniform concave layer for a nose covering I decided to do a circular shape. In fusion I made one that is protuding and one that is embedded. I was going to make the embedded hole deeper and wider then the extruding shape. Since it was a two piece I also added a step on one of the sides such that when put together the molds would wrap around eachother like a warm hug. I forgot to add a sprew and a vent in my fusion but I was planning on just cutting them in the mold.
Wax blocks
I felt like choosing a wax block was like choosing a wand from Harry Potter (I don't support JK Rowlings). I chose a barely used long wax block.MODS
We used a different mods program than we did most weeks, this week we used Rolland SRM-20 Mill 3D STL.- To get to it you go to mods website
- Programs
- Open server Programs
- Scroll down to olland SRM-20 Mill 3D STL
- Upload STl
- Rotate until correct side
- If in mm change mm to 1
- Start with rough cut, meaning using 1/8th and raising mill bit 1 more up once set it down
- Can choose either XY or YZ don't need to do both
- Then change to 1/16th mill bit and do finish cut by repeating last two steps
Oomoo 25
- Follow the box instructions
- Take the two solutions out of the box
- Make a mixture of both liquid parts in 1:1 proportion
- Mix until a single color
- Pour in mold and let sit for 75 min
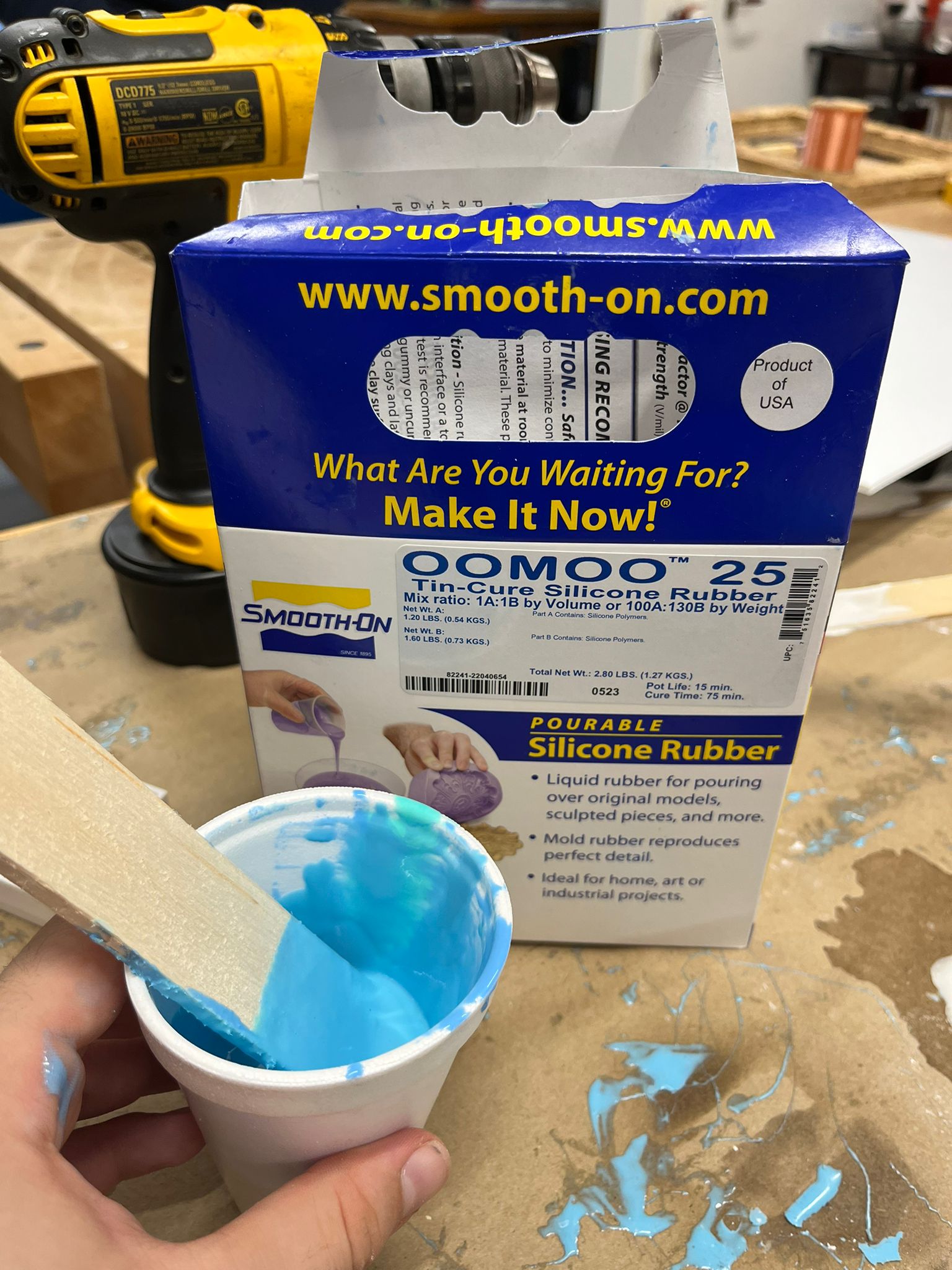